- Get link
- X
- Other Apps
Pioneers of Project Management: Deming vs Juran vs Crosby www. simplilearn.com
By Avantika MonnappaLast updated on Sep 27, 2019151347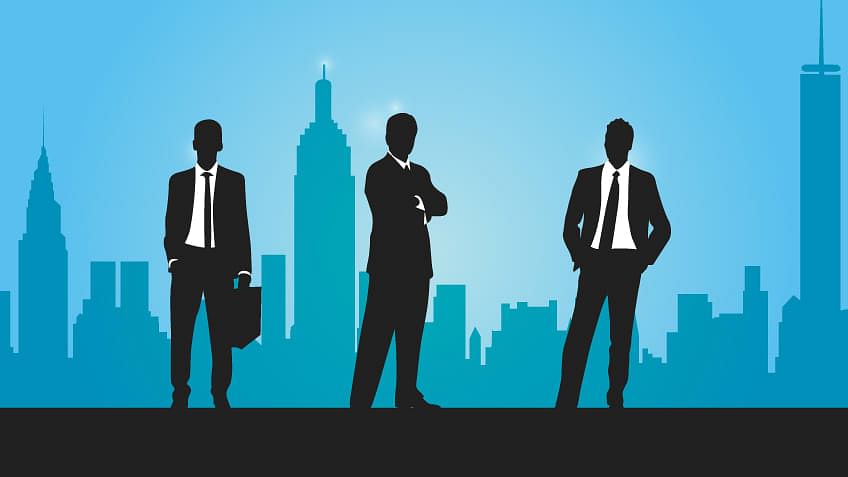
If you’ve been preparing for a Project Management exam, chances are the vast majority of what you have studied is directly or indirectly derived from the work of these three Project Management thinkers and theorists:
- W. Edwards. Deming
- Joseph M. Juran
- Philip B. Crosby
W. Edwards Deming
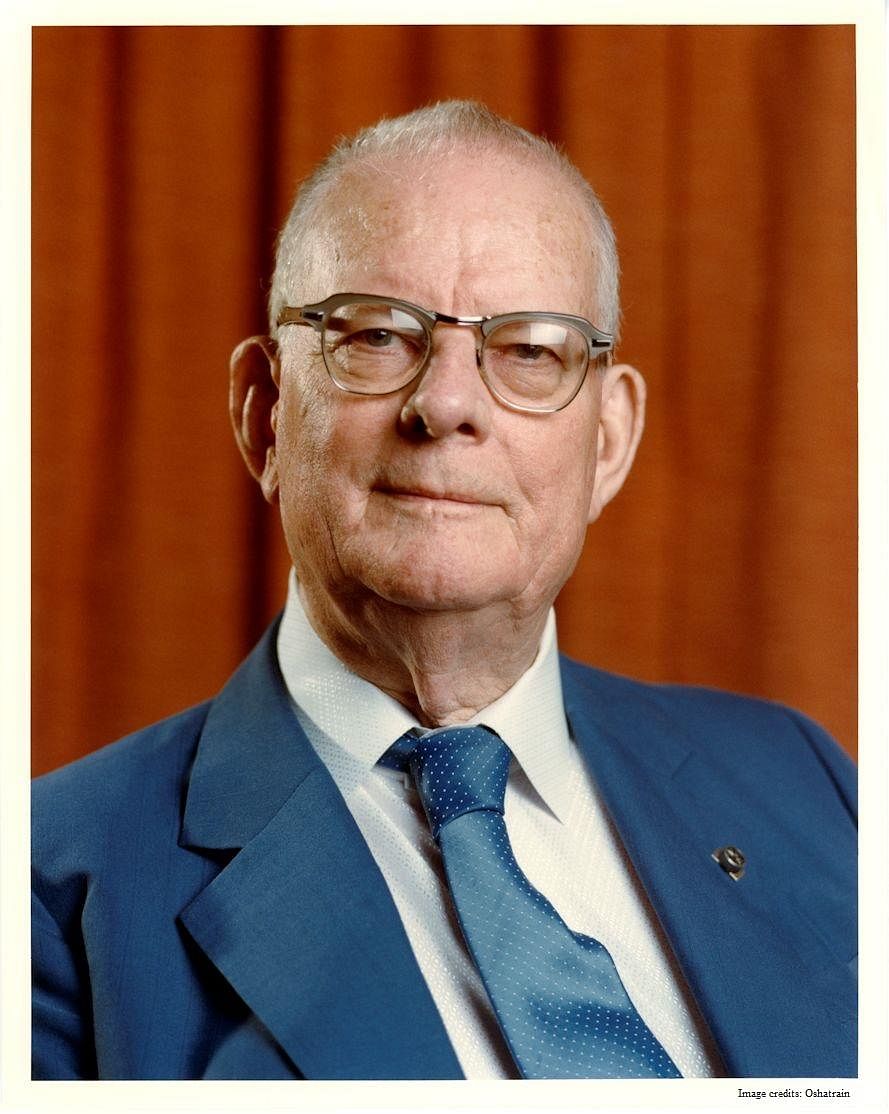
Who Was He?
Born in 1900, W. Edwards Deming was an American engineer, professor, statistician, lecturer, author, and management consultant.
What Was His Philosophy?
Deming opined that by embracing certain principles of the management, organizations can improve the quality of the product and concurrently reduce costs. Reduction of costs would include the reduction of waste production, reducing staff attrition and litigation while simultaneously increasing customer loyalty. The key, in Deming’s opinion, was to practice constant improvement and to imagine the manufacturing process as a seamless whole, rather than as a system made up of incongruent parts.
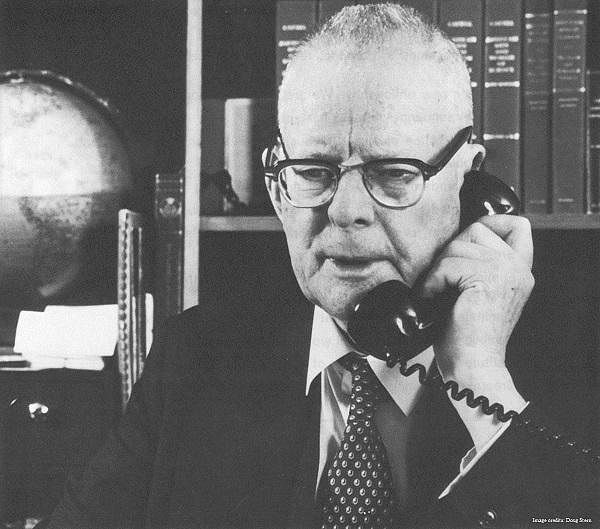
In the 1970s, some of Deming's Japanese proponents summarized his philosophy in a two-part comparison:
- Organizations should focus primarily on quality, which is defined by the equation ‘Quality = Results of work efforts/total costs’. When this occurs, quality improves, and costs plummet, over time.
- When organizations' focus is primarily on costs, the costs will rise, but over time the quality drops.
The Deming Cycle
Also known as the Shewhart Cycle, the Deming Cycle, often called the PDCA, was a result of the need to link the manufacture of products with the needs of the consumer along with focusing departmental resources in a collegial effort to meet those needs.
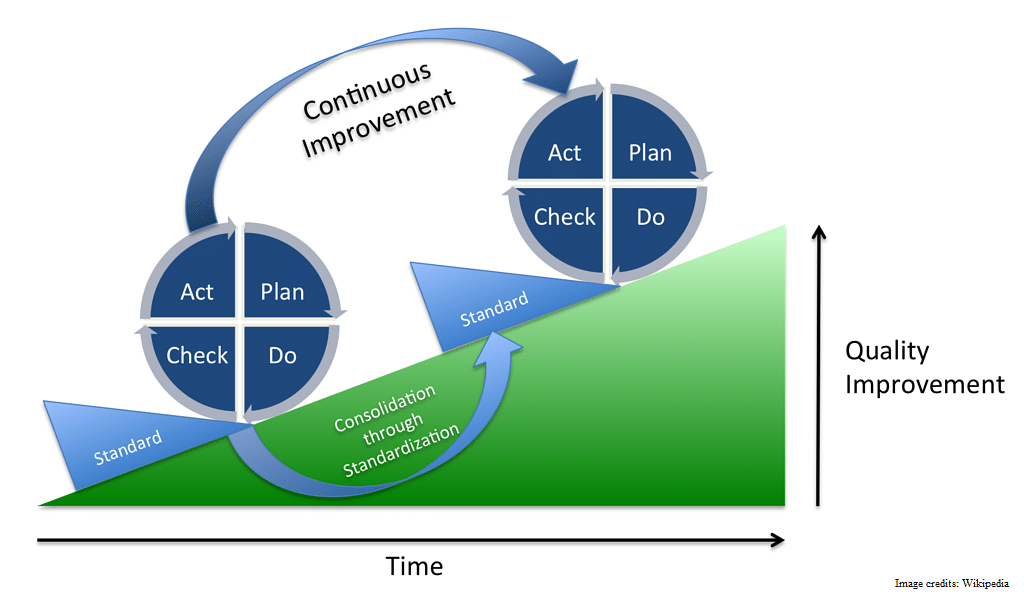
The steps that the cycle follow are:
- Plan: Design a consumer research methodology which will inform business process components.
- Do: Implement the plan to measure its performance.
- Check: Check the measurements and report the findings to the decision-makers.
- Act/Adjust: Draw a conclusion on the changes that need to be made and implement them.
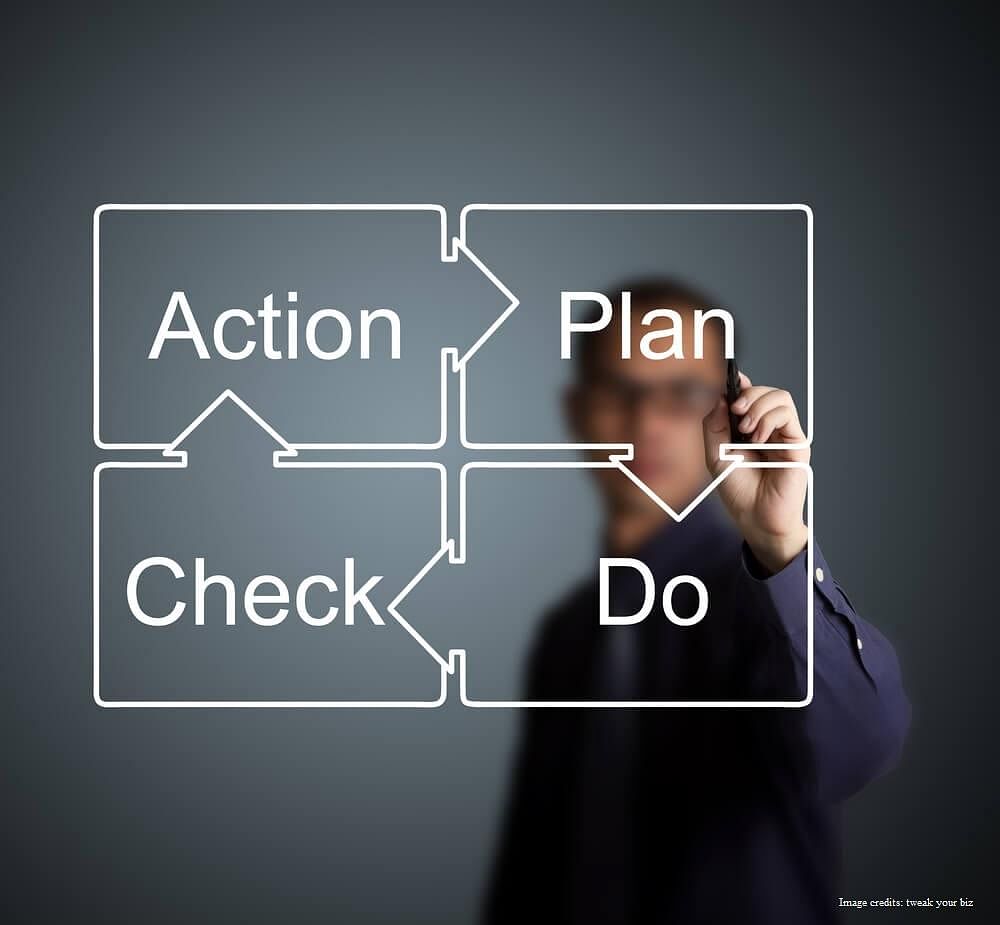
The 14 Points for Management
Deming’s other chief contribution came in the form of his 14 Points for Management, which consists of a set of guidelines for managers looking to transform business effectiveness.
- Create constancy of purpose for improvement of product and service
- Follow a new philosophy
- Discontinue dependence on mass inspection
- Cease the practices of awarding business on price tags.
- Strive always to improve the production and service of the organization
- Introduce new and modern methods of on-the-job training
- Device modern methods of supervision
- Let go of fear
- Destroy barriers among the staff areas.
- Dispose of the numerical goals created for the workforce.
- Eradicate work standards and numerical quotas
- Abolish the barriers that burden the workers
- Device a vigorous education and training program
- Cultivate top management that will strive toward these goals
The 7 Deadly Diseases for Management
The 7 Deadly Diseases for Management defined by Deming are the most serious and fatal barriers that managements face, in attempting to increase effectiveness and institute continual improvement.
- The inadequacy of the constancy of purpose factor, to plan a product or service.
- Organizations giving importance to short term profits.
- Employing personal review systems to evaluate performance, merit ratings, and annual reviews for employees.
- Constant Job Hopping
- Use of visible figures only for management, with little or no consideration of figures that are unknown or unknowable.
- An overload of Medical Costs
- Excessive costs of liability.
Are you a professional who is aspiring to be a project manager? Try answering this PMP® Practice Test Questions and assess yourself. |
Joseph M. Juran
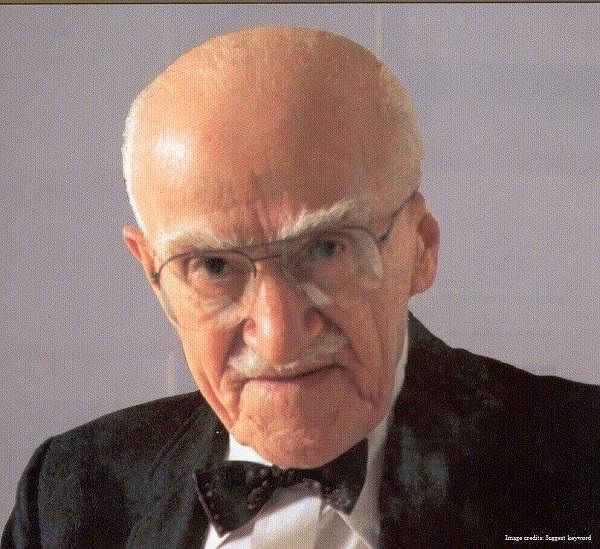
Who Was He?
Born in 1904, Joseph Juran was a Romanian-born American engineer and management consultant of the 20th century, and a missionary for quality and quality management. Like Deming, Juran's philosophy also took root in Japan. He stressed on the importance of a broad, organizational-level approach to quality – stating that total quality management begins from the highest position in the management, and continues all the way to the bottom.
Influence of the Pareto Principle
In 1941, Juran was introduced to the work of Vilfredo Pareto. He studied the Pareto principle (the 80-20 law), which states that, for many events, roughly 80% of the effects follow from 20% of the causes, and applied the concept to quality issues. Thus, according to Juran, 80% of the problems in an organization are caused by 20% of the causes. This is also known as the rule of the "Vital Few and the Trivial Many". Juran, in his later years, preferred "the Vital Few and the Useful Many" suggesting that the remaining 80% of the causes must not be completely ignored.
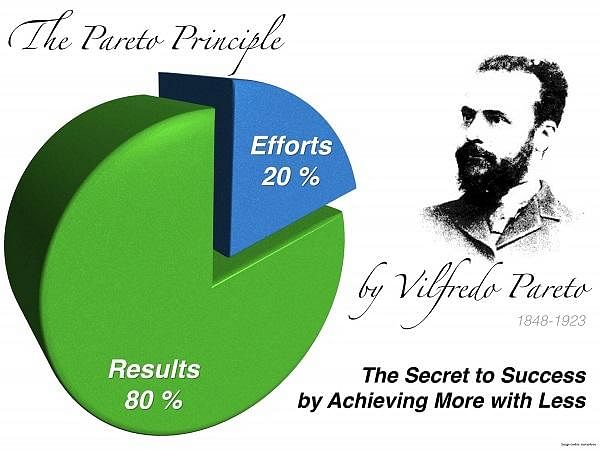
What Was Juran’s Philosophy?
The primary focus of every business, during Juran's time, was the quality of the end product, which is what Deming stressed upon. Juran shifted track to focus instead on the human dimension of Quality management. He laid emphasis on the importance of educating and training managers. For Juran, the root cause of quality issues was the resistance to change, and human relations problems.
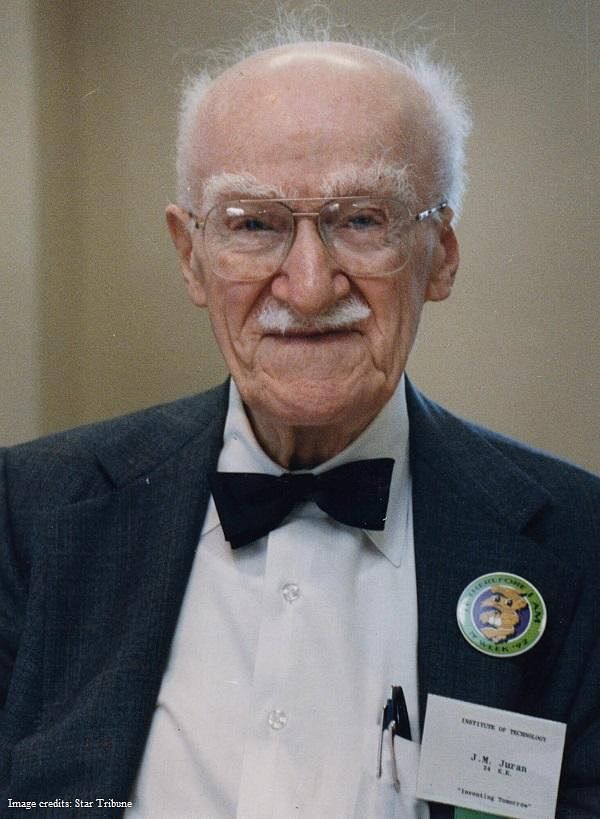
His approach to quality management drew one outside the walls of a factory and into the non-manufacturing processes of the organization, especially those that were service-related.
The Juran Quality Trilogy
One of the first to write about the cost of poor quality, Juran developed an approach for cross-functional management that comprises three legislative processes:
Quality Planning:
This is a process that involves creating awareness of the necessity to improve, setting certain goals and planning ways to reach those goals. This process has its roots in the management's commitment to planned change that requires trained and qualified staff.Quality Control:
This is a process to develop the methods to test the products for their quality. Deviation from the standard will require change and improvement.Quality Improvement:
This is a process that involves the constant drive to perfection. Quality improvements need to be continuously introduced. Problems must be diagnosed to the root causes to develop solutions. The Management must analyze the processes and the systems and report back with recognition and praise when things are done right.
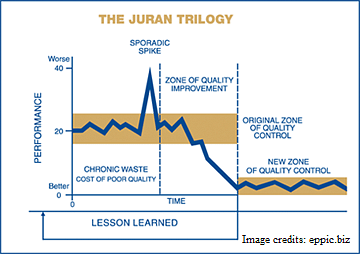
Three Steps to Progress
Juran also introduced the Three Basic Steps to Progress, which, in his opinion, companies must implement if they are to achieve high quality.
- Accomplish improvements that are structured on a regular basis with commitment and a sense of urgency.
- Build an extensive training program.
- Cultivate commitment and leadership at the higher echelons of management.
Ten Steps to Quality
Juran devised ten steps for organizations to follow to attain better quality.
- Establish awareness for the need to improve and the opportunities for improvement.
- Set goals for improvement.
- Organize to meet the goals that have been set.
- Provide training.
- Implement projects aimed at solving problems.
- Report progress.
- Give recognition.
- Communicate results.
- Keep score.
- Maintain momentum by building improvement into the company's regular systems.
Here's the video of our course on Introduction to Project Management Certification Training. Hope you find it beneficial.
Philip B. Crosby
Who Was He?
Born in 1926, Philip B. Crosby was an author and businessman who contributed to management theory and quality management practices. He started his career in quality much later than Deming and Juran. He founded Philip Crosby and Associates, which was an international consulting firm on quality improvement.
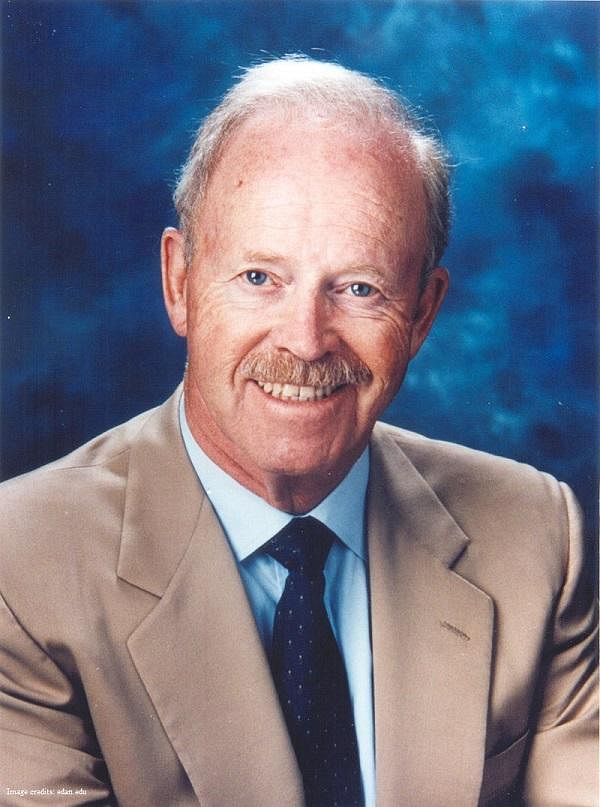
His Philosophy/Theory
Crosby's principle, Doing It Right the First Time, was his answer to the quality crisis. He defined quality as full and perfect conformance to the customers' requirements. The essence of his philosophy is expressed in what he called the Absolutes of Quality Management and the Basic Elements of Improvement.
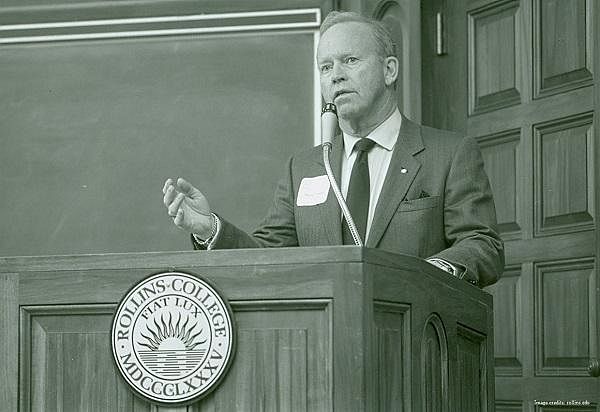
The Absolutes of Quality Management
Crosby defined Four Absolutes of Quality Management, which are
- The First Absolute: The definition of quality is conformance to requirements
- The Next Absolute: The system of quality is prevention
- The Third Absolute: The performance standard is zero defects
- The Final Absolute: The measurement of quality is the price of non-conformance
Zero Defects
Crosby's Zero Defects is a performance method and standard that states that people should commit themselves too closely monitoring details and avoid errors. By doing this, they move closer to the zero defects goal. According to Crosby, zero defects was not just a manufacturing principle but was an all-pervading philosophy that ought to influence every decision that we make. Managerial notions of defects being unacceptable and everyone doing ‘things right the first time’ are reinforced.
The Fourteen Steps to Quality Improvement
- Make it clear that management is committed to quality for the long term.
- Form cross-departmental quality teams.
- Identify where current and potential problems exist.
- Assess the cost of quality and explain how it is used as a management tool.
- Improve the quality awareness and personal commitment of all employees.
- Take immediate action to correct the problems identified.
- Establish a zero-defect program.
- Train supervisors to carry out their responsibilities in the quality program.
- Hold a Zero Defects Day to ensure all employees are aware there is a new direction.
- Encourage individuals and teams to establish both personal and team improvements.
- Encourage employees to tell management about obstacles they face in trying to meet quality goals.
- Recognize employees who participate.
- Implement quality controls to promote continual communication.
- Repeat everything to illustrate that quality improvement is a never-ending process.
The Quality Vaccine
Crosby explained that this vaccination was the medicine for organizations to prevent poor quality.
- Integrity: Quality must be taken seriously throughout the entire organization, from the highest levels to the lowest. The company's future will be judged by the quality it delivers.
- Systems: The right measures and systems are necessary for quality costs, performance, education, improvement, review, and customer satisfaction.
- Communication: Communication is a very important factor in an organization. It is required to communicate the specifications, requirements and improvement opportunities of the organization. Listening to customers and operatives intently and incorporating feedback will give the organization an edge over the competition.
- Operations: a culture of improvement should be the norm in any organization, and the process should be solid.
- Policies: policies that are implemented should be consistent and clear throughout the organization.
Questions on Deming’s, Juran’s, and Crosby’s Theories in Certification Exams
Here are a few sample questions, courtesy the Tutorial Point and Cornelius Fichtner
A. According to Deming and Juran, most of the quality problems that exist are due to a defect or failure in processes that are controlled by:
- The project manager.
- The procurement manager.
- The management.
- Stakeholders.
Hint: The quality policy is defined according to an organization's top management.
B. In the Shewhart and Deming cycle, the letters P D C A stand for:
- Purchase, delivery, cost, and acquisition.
- Prevent defects caused by anyone.
- Plan, do, check, and act.
- Please don.t cause accidents.
Hint: Deming Cycle is also known as Deming Wheel or Shewhart Cycle. It uses the 4-step method for continuous improvement.
C. Cultural resistance is the root cause of quality issues according to whom?
- Deming
- Malcolm Baldridge
- Juran
- Shelby
Answers:
A. 3, B. 3, C. 3
This article is part of a series on project Management: plug gaps in your knowledge with the complete set of articles!
- Get link
- X
- Other Apps
Comments
Post a Comment